Mold heating equipment
2024-03-21
Mold heating equipment, 4 thermocouples, 1 infrared temperature measurement
At present, the common electric heating oil bath oven is used for mold heating, and its main principle is to heat the mold through the heat radiation of the oven wall and the heat exchange between the hot air and the mold. Ordinary electric heating oil bath ovens have disadvantages such as long heating cycle, low heating efficiency, high requirements for operators’ experience and high energy consumption. As a heating technology, High frequency induction heating machine heating has the characteristics of precise heating depth and heating area, high heating power, fast heating speed, high efficiency, low energy consumption, easy control of heating temperature, and easy automation of the heating process. Since the 1930s In the 1980s, since induction heating technology was widely used in industrial production, it has shown more and more extensive application prospects in many industrial fields so far. At the same time, the investment cost of induction heating equipment is low, especially the temperature control is precise. Applying it to the powder thermocompression molding process will greatly improve the quality and production efficiency of molded products.
1. Special equipment for three-station mold induction preheating
Special equipment for three-station mold induction heating preheating: continuous induction heating, preheating a mold about every 60 seconds, mold preheating is carried out by three-station integrated intelligent induction heating equipment for temperature closed-loop control heating, and the mold is preheated to 150 °C for assembly. The temperature difference between the outer wall of the mold and the inner wall of the mold is small, so that the overshooting tendency of the internal temperature of the mold is reduced, the temperature is stable and easy to control during the heating process, and the production efficiency and product quality are improved.
Features:
1) Induction heating preheating method: high efficiency, fast preheating speed, multi-stage temperature control in the preheating area, uniform preheating temperature, and no oxidation;
2) The second-generation DSP intelligent induction heating equipment is adopted, and the double closed-loop control of power and temperature is adopted. At the same time, it can realize the function of temperature curve control, 4-point temperature display and protection function. During the heating process, the overall temperature of the mold does not exceed the set temperature ± 3°C; when the heating ends, the temperature difference of each part of the mold is less than 5°C; the heating power is adjustable, and the feedback adjustment can be made according to the actual measured temperature of the mold, and the heat preservation function can be realized.
3) On-line thermocouple closed-loop control system, high temperature control accuracy, fast control speed, real-time display and record of temperature.
4) With real-time temperature alarm function, alarm signals are sent out in time when abnormalities occur in the production line, including high and low temperature alarms, heating overtime alarms, etc.
5) Professional online tooling and positioning fixtures ensure accurate positioning of each mold during heating, temperature uniformity, and preheating speed.
6) It has the functions of constant power, constant current, and constant temperature arbitrary switching combination, which is convenient for heating applications with different loads.
7) It has remote control and internal control operation mode switching, which is convenient for switching control modes.
8) With load matching indication function, it is convenient and intuitive to guide the selection of load matching.
9) It has the function of recording the alarm state of the equipment, which is convenient for querying the historical data of the equipment.
10) It has a hierarchical login function for administrators and operators to prevent unauthorized personnel from adjusting the heating process.
Intelligent DSP induction heating operation status and parameters such as voltage, current, power, frequency, etc. are collected and monitored in real time. At the same time, these states can be directly connected to the centralized control network through the internal communication interface of the power supply, and the required parameters can be transmitted to other controllers such as industrial computer, numerical control system, notebook computer, remote control center, etc. to realize the needs of the Internet of Things in the workshop.
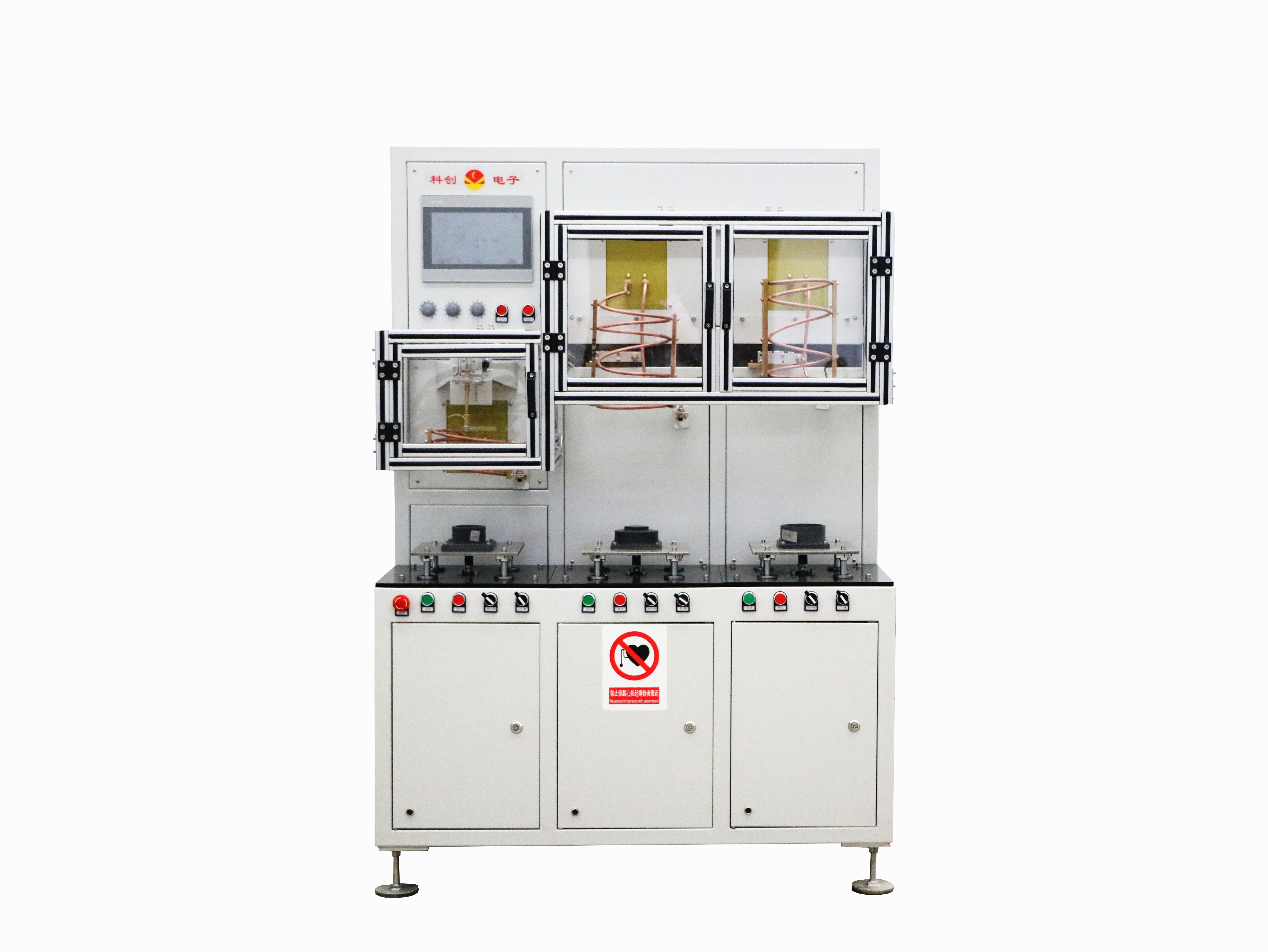